by Richard Post
The idea was introduced like a lot of things at the Denver Fly Fishing Show—in the found minutes between helping folks try on waders, extolling the virtues of various products and the waters where we ply our trade, and catching up with old friends and customers.
Jay found himself in our booth and posed the question, “So do you want to go steelheading?” I don’t remember exactly how I responded, but I imagine it was some sort of offhand colloquial idiom amounting to, “Don’t threaten me with a good time.” A few months later Parker and I are on a plane heading to Woodland, Washington for a tour of the G.Loomis rod factory. I have been to this part of the world but have never flown into Portland, Oregon. The volcanoes are striking, monuments of classical mountain geography, brazenly white against the verdant ridges and lushly carpeted rolling hills. The mighty Columbia and her oxbows straighten with the plane’s descent and the foothills and shoulder of the great volcano are overtaken by the forest view and the big, broad river.
Wheels down. Jay and Red, our G.Loomis hosts for the weekend, pull up to the curb. Warm greetings and luggage help are exchanged and we set out across the Columbia, coming to rest at an island-inspired eatery overlooking the water. Jake, the last member of our G.Loomis crew, has a table for us. Drinks as wildly colored as steelhead flies and watered with rum are spread out among the beers and oyster shooters. The sun kept on its steady path westward and downward as the big river shimmered against the churning, splashing and nefarious carrying-ons of a curiously large sea lion colony. Red filled us in on the backstory of the Columbia River’s young and unfortunately burgeoning sea lion population, a byproduct of the dams and yet another variable working against anadromous fish of the Pacific Northwest.
On to the casino hotel for the night. A huge lobby with some fine looking artisanal wooden oars caught my eye bracketing the entryway to the flickering lights of the slot machines and the subliminal ching-a-ling of a cash register. A welcomed sleep found us, a commodity we would take for granted in the coming days.
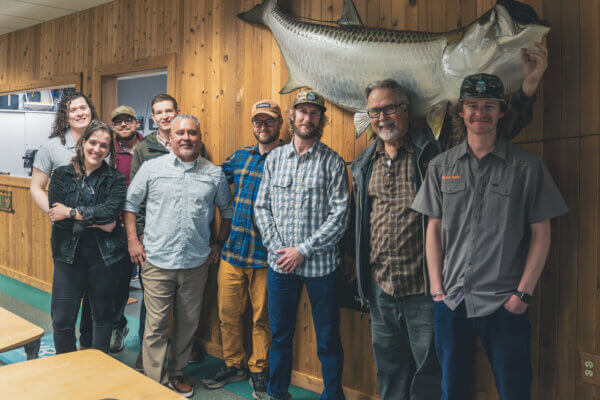
Not far at all from Vancouver, Washington is the city of Woodland and the G.Loomis manufacturing facility. There’s a pickup or four in the employee parking lot, a minty green deep vee with a forward cabin and a patina telling of her willingness to do her honest work, waiting for her captain to come off shift. Through the doors, you are warmly greeted by smiling employees and an inviting floor plan. Glass cabinets on the left display classic catalog covers, signed photos and “grip and grins” of former presidents, Hall-of-Famers and all manner of fishing personalities. Fish mounts add to the ambiance and a world-record tarpon with the 12-weight that landed her keep pulling at your eyes. Rods of all manner are neatly racked in nearly every space. I love it. Rod racks attached to working desks, the glow from the monitors dancing off the blanks. Some are repairs, some current models, some are one-off rods that you couldn’t really even call a prototype, and I’ve got to look at all of them.
We move into the conference room to meet the whole team and hear from the source about what goes into making a G.Loomis rod. For those who aren’t wholly aware of the rod building process, there is a tremendous amount of effort put into the science of rod design and material construction at every level. Rod handle prototypes are printed on a 3D printer and ready to actually test and fish on the water. Thread wrap colors go through a process of UV testing to ensure they won’t fade or weaken from sun exposure. Cork handles can be milled on the spot via an automated CNC mill and tested for hand fit. Rod blanks and wrap colors are laid on a wall just like we line up soft goods to compare pallet choices.
Some of the finished blanks are selected to donate their complete form to the pursuit of higher knowledge and new data points. The gallows for these brave blanks is a roughly 15 foot high by ten foot long metal box. A white deflection chart against the back wall of the thing, a metal bar running vertically supports a traveling device that secures the butt of the rod. A horizontal rail holds a little wheeled swivel snap ring, large clear safety plastic doors bearing the scars and scuffs from previous judgements insulate the observers without masking the spectacle.
The door is opened, a butt section is secured into the vertical traveler, a heavily taped looped tip is held fast by the swivel clip on the horizontal track and the rod is left bent over in an uncomfortable repose as the doors close. The machine begins its work on the blank as the vertical traveler rises higher, the poundage increases and the blank seems to become almost elastic until, “Snaaaap, pop, rattle, bang, bang, baaaaang,” and then quiet. A little puff of nearly vaporized resin settles, and the wagers are checked. A 5-weight ought to break around 5 pounds, a 7-weight around 7 pounds and so on, roughly an extra pound of pressure as you go up in line weight. We put a big bluewater rail rod on the rack and it exploded at around 68 pounds. They even let me take another of those bluewater blanks, attach the tip to the swivel clip on the horizontal rail and see how much pressure I could apply upward. I would have to be told to leave this thing alone if I worked here.
The broken rod is the point of this whole exercise. The engineers examine the data of the failure and investigate the physical break in a criminal sense as well. If they suspect a habitual weakness in a blank, they rack it and expose the weakness. “Wham! Crack! Pop!” They then take the information back to design level and reinforce the blank above and below the break. A small change in the design of the cut essentially smooths out the stress point by building a bridge to remove the focus of the pressure on the weak spot. Brilliant! Then back to the rack to test the theory, the end goal being to get the rod to break when and where they expect it to. This was the aspect of rod design that I could see and feel. My understanding of rods and rod design comes from a sense of feeling and a place that is more artistic than scientific. I can tell you what the rod is doing and why it is doing it or reacting in the manner it is, but I cannot tell you why the rod is doing it in relation to the specific materials. This is real science and certainly above my schooling. Every aspect of the rod build is scrutinized in this manner.
When you cross the threshold from the break room onto the factory floor, you are greeted with a hum of activity. Rods and rods along with a wall of mandrels steel your gaze upward and out. Machines of all manner neatly and completely occupy the factory floor. Myriad carts, racks and various shelving units all stand orderly and awaiting their specific lot.
The floor is spotless to the degree that I’d pick up a dropped ice cream cone and feel more pity for the floor than my headless treat as I set the mess back atop the cone. A green path indicates the safety area around the factory floor and follows the path of rod production.
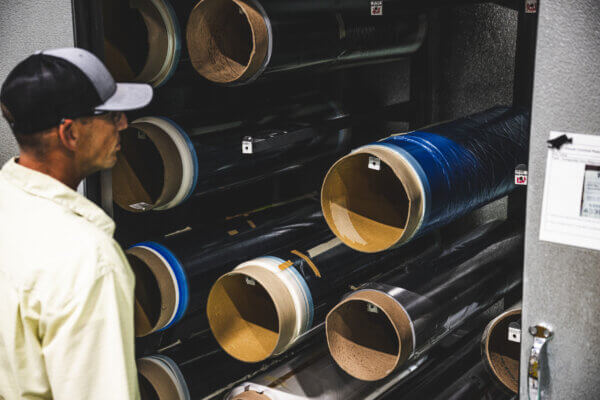
The first step in production is cutting out the graphite material in a pattern. While some patterns may be cut by hand, the majority are cut from large rolls of material on a CNC laser cutter. The bulk rolls of material are stored and managed in a specific manner to eliminate water from condensation and humidity, and to regulate temperature: consistency and reduction of variables. The laser zaps out the patterns and they are collected onto their shelf. A quick trip to a vast vacuum sealer to eliminate air and now the scalene obtuse forms are rigid and ready to be tacked and rolled.
A mandrel comes off the storage rack and is warmed slightly for material adherence. The mandrels are the exoskeleton of the fly rod, the forms that the graphite is rolled around, and they are handled with great care. The tips of the steel mandrels are obviously very fine. Any bend out of true in the mandrel results in a crooked rod. An assortment of brass hammers and leather pads are the only cure for an ailing mandrel along with a skilled hand. Over to the space adjacent to the rolling table. The patterns are laid out and measured along the mandrel, tacked into place and set under the rod roller. Hydraulic levers lift and fall with a confident whift as the machine calibrates, then the whole apparatus comes forward several inches in less than a second. The sound of pressure releasing and the graphite is now formed around the mandrel. The multi-taper technology comes from the rod roller conforming to the specific changes in taper and ferrule connection. Air and space are eliminated for a smoother connection to the mandrel. Now the rolled blank either goes to the cello wrap machine or the Spiral X machine. Both occur in the same space, but a rod with Spiral X has already undergone one twist through the Spiral X machine before the rod roller. This thin graphite material goes on first in one direction, graphite patterns are laid and rolled, then the Spiral X material goes on in the opposite direction, a truly remarkable process that allows for stronger blanks with less material overall. These rods have a lightness and feel that is second to none and to watch the efficiency and exactness of the process firsthand is remarkable. Cello wrapping is next as the rolled blanks spin and twist up along the machine. Tall, wheeled metal racks await the blanks. They are hung by their tip and secured by a spring on the floor for tension. Now into the oven where they will cook and cure and then the resting oven before mandrel removal.
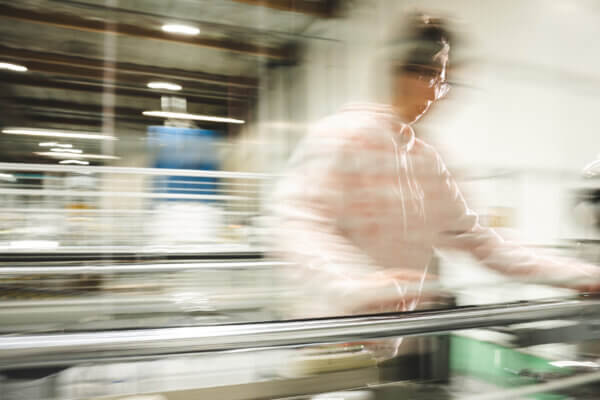
Mandrel removal is hands on and gritty. The butt of the mandrel is inserted into a hydraulic puller and if all goes well, the mandrel is smoothly but not quietly pulled from the now formed rod. The amount of force required is not surprising when you think about it, but from the perspective of a handler of fishing rods, it made me nervous. A satisfying resonance as the pulled blanks rattle down to their catchment and the hydraulic pump exhales. Onto the cello unwrap machine—an ingenious device that removes the cello wrap with negative pressure, twisting it off the blank in the opposite manner it was applied. Neat little jigs hold several rods and guide them along the ordered rattly process. Now the blanks look like a rod, raw gray graphite with neat little concentric rings running up. Sanding requires a skilled hand. Speed and pressure are adjusted to the size of the blank and with gloved hands closer to the wet sander than I would care for, the section is whipped through in a buzz and spray and now you have a matte grey smooth blank. We were shown examples of tolerances and burns where the sander cut into the graphite, what they’re looking for but hoping not to find. Each blank or section is put under a lighted magnifying glass and examined along the length. The sanding tolerance they strive for is .001, just the rings. I saw it happen and that’s all they take. It was very cool to see how precise the process was, watch the blanks rattle out and watch a skilled eye pass judgement on each one.
Time to fit the ferrules. G.Loomis has created a standard for their ferrule sizing for the tip to the second section and the second section to the third. They can achieve this with the precision of their multi taper rod roller without adding or removing any material. With a set of jigs, they check and fit every ferrule to the standard for that model. This is not something that all fly rod consumers know, but you cannot take the tip section from one Model XYZ 905 and swap it with another Model XYZ 905. They will be different, some of you will try this, and it illustrates how individual most rods are. It also means that repairs take longer because a replacement section must be built to fit that individual rod, rather than a rod model. For Loomis customers this means that they can break a tip section and know that the replacement tip will fit without having to send in the whole rod for repair, because Loomis makes all of their tips for that model fit to a standard. The rodsmith who was working the ferrule fit station had that measured hand and calculating stare of a craftsman and a fisherman. I enjoyed watching him eyeball a blank and reach for the exact place of the correct jig with measured efficiency. The ferrule standard and tip replacement program are exactly that, measured efficiency. Repairs happen more quickly, it takes the factory less time to produce tip sections that are all the same, and the ferrule fitting process is more black-and-white. There are no mixing and matching sections to achieve the proper fit. Take the piece, measure it against the standard and fit the sections.
The rods are now ready for paint. A long, glassed corridor two levels high houses the climate-controlled paint room. Blanks are dipped into vats of paint recessed in the floor and straight onto the rack. Various colored blanks hang down and travel along a metal conveyer belt at a snail’s pace, side by side, each making a daylong pirouette as they slowly cure. G.Loomis uses water based paints that have a longer drying time but a stronger bond without the use of solvents. Screen printing the logo is a step that most would think about as easy as they come. Not the case. The correct pressure must be adjusted along all sides of the rod, mess up, wipe it off and try again until it is perfect. There is much more touch and feel required than I anticipated in this guess-and-check process.
Handle assembly is next up. The handle reamer does just that. The handle assembly is pulled through, flinging and screaming cork dust, and the resulting space is the diameter of the graphite blank to be inserted. The drill bits were made by milling teeth into the butt ends of spent mandrels. Very clever. Handles are glued using liberal amounts of epoxy and lined up on a table studded with adjustable 3D printed jigs, precise and repeatable.
I got to watch some bass rod handles and large salmon trolling rod handles get glued on. Handles are on, rods are painted and screen printed, now they go out to wrap for guides and thread wraps. Once they return, the rods go to a station to have the guides lined up via a laser and computer combination. A laser and a camera are calibrated to one another, and the image appears on a monitor. This whole assembly slides on a rail the length of the rod and is controlled by a handle. The apparatus slides along the length of the rod and each guide is lined up and adjusted true. The guides are now straight and true, and the rods enter a bank of drying wheels. A gameshow-like appearance, these long clear tubes with all sorts of rods turning around one another. A small device holds and spins a rod at the base of the drying wheel for epoxy application; as the rod spins the epoxy is ladled on. The excess falls off as it spins, and the freshly epoxied rod goes onto the big wheel with its brethren to cure.
Ferrule plugs are the final step before inspection. Inspection is carried out by a thorough and scrupulous corps. Any inconsistencies are measured against actual examples of intolerances. In the case of epoxy height, they have a jig they place over the wraps, if the jig rocks, the wraps are too thick. This group had some of the best banter and I got the sense that this station was one of the spots you had to earn, the final say and last point of scrutiny before they are ready to be sold.
We blew up rods in the large white rod destroyer with the research and design team after we made it past final inspection. Rods built anew and rod blanks cast asunder in the pursuit of inquiry. I cannot tell you how much fun it was to witness the grotesque rod angles achieved at the moment of failure, and to see Steve Rajeff’s eyes light up and his step lighten when we went over to the rod breaking machine.
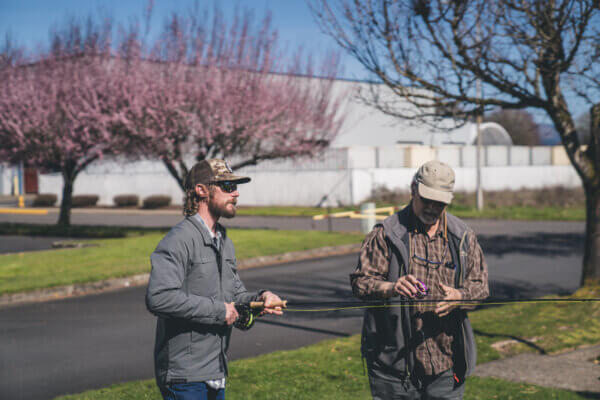
We conjured up a couple of minutes to cast on the side lawn with Rajeff and some of the crew before we had to hit the road. It’s always great to trade some lawn casts with one of the best to ever do it. We had thoroughly run past our time by now and had plans to get up the coast and catch the sun as it dipped to hide behind the big ocean for the night. Pried away, I wiped my brow, shifted to our fishing plans, climbed into the rental and headed north.
[G.Loomis Chronicles, Part 2: Steelhead Country]
[G.Loomis Chronicles, Part 3: The Learning Curve]
[G.Loomis rod pages]